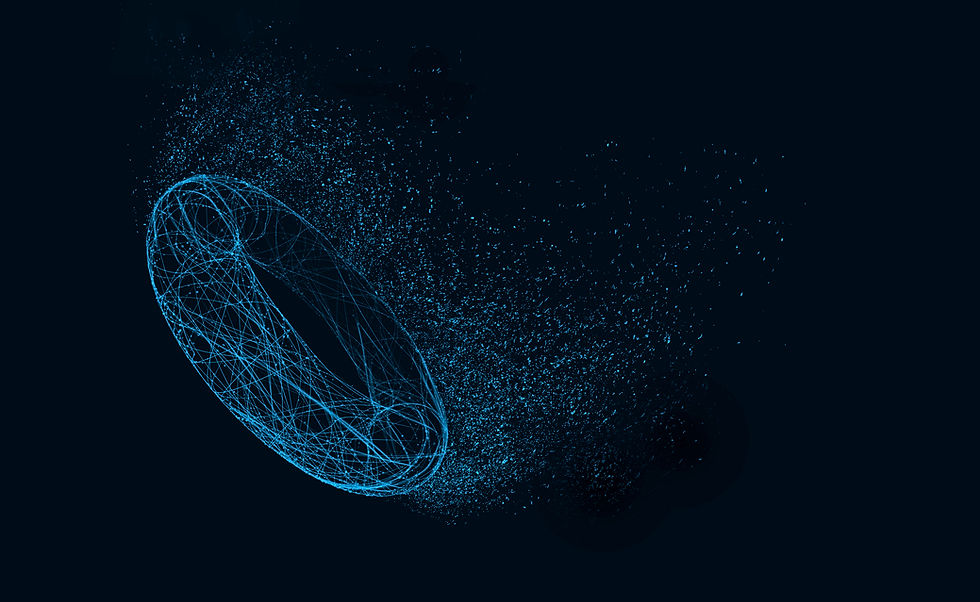
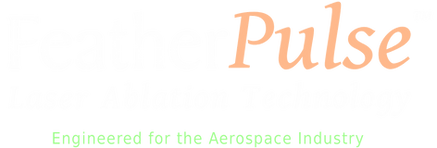
Innovative Laser Tech
Enhancing Aircraft Maintenance Efficiency
Our Technology
FeatherPulse Laser Ablation Technology: Precision Cleaning for Aerospace Materials
1. Platforms & Key Specs
-
FeatherPulse Compact (FP‑300c / FP‑500c)
-
Average Power: 300 W / 500 W at 1 064 nm
-
Pulse Duration: 100–350 ns
-
Form Factor: Handheld or benchtop, ideal for spot repairs and on‑wing maintenance
-
-
FeatherPulse Robotic (FPr‑300r / FPr‑500r / FPr‑1000r)
-
Average Power: 300 W, 500 W, or 1 000 W at 1 064 nm
-
Integration: Six‑axis cells with galvo‑scan heads, vision‑guided path planning
-
Throughput: Up to 800 mm³/min per arm on heavy deposits
-
2. Photothermal & Photomechanical Advantages
-
High Peak Intensity: Nanosecond pulses concentrate energy into rapid thermal expansion and shockwaves, spalling away coatings, sealants, corrosion products, and CMAS without gouging the substrate.
-
Minimal Heat‑Affected Zone (HAZ): Typical HAZ ≤ 100 µm—orders of magnitude smaller than abrasive or chemical methods—preserving grain structure and mechanical properties of titanium, nickel superalloys, and aluminum alloys.
-
Wavelength Selectivity: Infrared absorption contrasts between organics (sealants, oils), oxide scales, and base metal ensure contaminants absorb preferentially, leaving underlying alloys intact.
3. Aerospace‑Grade Materials & Contaminants
-
Thermal Barrier Coatings (TBCs):
-
Selective Strip‑Back: Precisely remove spent YSZ topcoats and bond‑coat spall without damaging the underlying MCrAlY layer—preparing for re‑spray.
-
-
Corrosion & Oxide Scales:
-
Oxide Spallation: Photothermal ablation lifts mill-scale and high‑temperature oxides from compressor and turbine vanes, restoring surface finish.
-
-
Sealants & Adhesives:
-
Ablation of Rubber/Polymeric Sealants: Clean away degraded sealant films from flange joints and rib‑seal areas with sub‑micron control, avoiding mechanical scraping.
-
-
Paint & Primer Removal:
-
Controlled “Micro‑Etch”: Strip thin primer layers without substrate pitting—eliminating sanding and chemical strippers.
-
4. Process Control & Automation
-
Vision‑Guided Scan Patterns: 3D laser profiling maps blade contours; AI‑driven algorithms compute optimal overlap and scan speed for uniform material removal.
-
Real‑Time Feedback: In‑line power monitoring and back‑scatter sensors adjust pulse energy on‑the‑fly to maintain constant ablation depth—even on variable geometry.
-
Multi‑Pass Strategies:
-
Low‑Power Pass: Remove organics and light films.
-
High‑Power Pass: Strip tenacious oxides and CMAS.
-
Finish Pass: “Polish” surfaces for < 1 µm roughness.
-
5. Technical Benefits
-
Extended Component Life: By avoiding mechanical damage and excessive heat, FeatherPulse preserves substrate metallurgy and prolongs service intervals.
-
High Throughput: Up to 800 mm³/min on FP‑1000r cells means entire blade sets can be cleaned in under an hour.
-
Versatility: One laser head handles a range of tasks—from deep‑scale removal on hot‑section parts to fine‑film stripping on composite fairings.
-
Reduced Fixturing Complexity: Fiber‑delivered beam and small‐spot galvo optics access narrow ribs and platform slots without complex tooling.
-
Repeatable Quality: Digital recipe storage ensures identical results across shifts and facilities, simplifying certification and audit trails.
FeatherPulse Laser Ablation delivers the ultimate balance of power, precision, and process intelligence—enabling aerospace MRO teams to clean, prepare, and refurbish critical components faster and safer than ever before.

Our laser technology is based on the
JPT YDFLP-CL2 architecture
Updated ZBTK control system for accommodating our FeatherPulseTM power conditioner which enhances its precision, accuracy and increased scanning speed
Lighter, faster galvo ablation head
The FeatherTronicTM Power Conditioning Inverter/Power Supply with Software Management
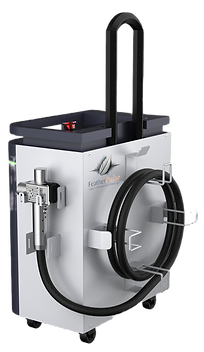



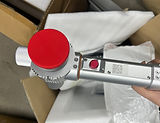

Scientific Study
Corrosion and Wear Performance of Aircraft Skin after Laser Cleaning
[1] [excerpt]"The fretting friction and wear performance of aircraft skin rivet holes after laser paint stripping with different energy densities was studied, the friction and wear performance of other parts of the skin were studied and compared with mechanical grinding and laser paint stripping. The results showed that the laser did not reduce the friction and wear performance of any part of the aircraft's skin surface. The residual stress, micro-hardness, and corrosion performance of the aircraft skin surface after laser paint stripping were studied. Compared with the mechanical lapping and laser paint stripping method, it proves the laser will not reduce the hardness and corrosion resistance of the aircraft skin."
Version of Record: https://www.sciencedirect.com/science/article/pii/S0030399220311087
© 2020 published by Elsevier. This manuscript is made available under the Elsevier user license https://www.elsevier.com/open-access/userlicense/1.0/
Our Partners
Collaborative Relationships
We value our partnerships with industry leaders, working together to deliver high-quality services and innovative solutions. These collaborations enable us to provide comprehensive aerospace maintenance and refurbishing services, ensuring excellence and client satisfaction.

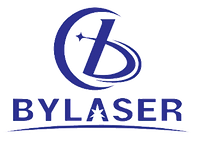
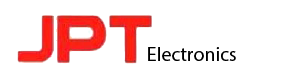
